Tungsten Blades: A Cut Above the Rest
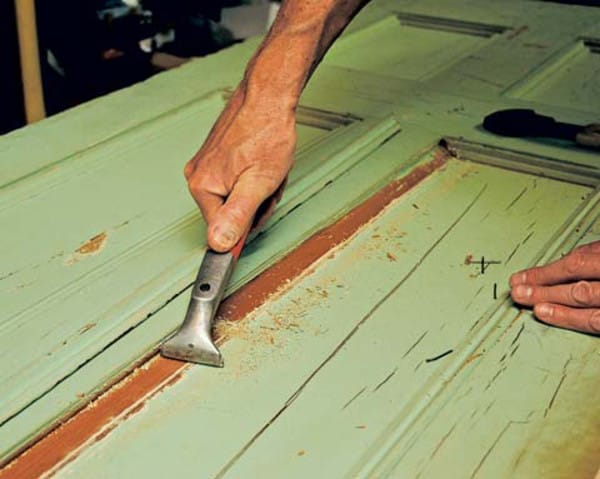
Choosing the correct material for your blades can often be a confusing task. Ultimately the answer comes down to the blade’s intended purpose and resulting necessary qualities. This article will look at one of the most common materials, Tungsten, analysing its properties and uses and the overall effectiveness of a Tungsten blade.
What Is Tungsten?
Tungsten is the 74th element in the Periodic table. It is one of the strongest metals on Earth, with the highest melting point of all metals – melting at the temperature of 3,422°C!
However, the metal is incredibly dense in its purest form, making it brittle and tough to work with. Despite its impressive properties, the hardness value of Tungsten is surprisingly low at 7.5 on the Mohs scale. This value is similar to that of hardened steel and is soft enough to be cut using only a hacksaw.
Because of this, Tungsten is most commonly used as an alloying material. Combined with other metals to benefit from the physical and chemical properties of each of them. By alloying Tungsten, you still benefit from the heat resistance and overall toughness, yet the alloy is much more useable and suited to a broader range of applications.
What Is Tungsten Carbide?
The most common alloy of Tungsten is Tungsten Carbide. Formed by mixing Tungsten powder with powdered Carbon, this chemical compound has an increased hardness value of 9.0 on the Mohs scale – comparable to the hardness value of diamond.
The Tungsten Carbide alloy also has an incredibly high melting point of 2200°C. Therefore, compared to Tungsten in its pure form, Tungsten Carbide is more widely used as it has the qualities of Tungsten with the added benefits of Carbon.
Application Of Tungsten Carbide
With such great heat and scratch resistance and durability, Tungsten Carbide is most commonly used in industrial cutting applications, i.e. machine knives and blades.
Tungsten Carbide has been utilized in this industry for almost a century. Here the Tungsten Carbide is used to cut carefully controlled shapes over and over again. Tungsten Carbide has been chosen as the best, most appropriate material in this scenario. Its durability and wear-resistance allows it to cut intricate shapes repeatedly without receiving any damage.
The high heat resistance of Tungsten Carbide also makes it able to spin at high speeds for long periods of time, without overheating and causing damage. This is why Tungsten Carbide is also used in the production of wear-resistant components, for example, saw and drill tips and crushing machinery.
Tungsten Carbide Vs Steel
Commonly used for many of the same applications, Tungsten Carbide and Steel are often closely compared. There is much debate in both the machine cutting industry and the knifemaking community for which material is best.
While most tool steels have incredibly high wear resistance, Tungsten Carbide does win the award for having the greatest wear resistance out of the two. This value is essentially used to describe how hard it is to remove the material through wear. This quality is essential in the machine cutting industry, meaning Tungsten Carbide wins a point here.
So, whether you’re embarking on a grand renovation project or simply enhancing your living space, remember that the quality of your tools can define the quality of your work. Choose Koing’s Tungsten Blades – because your craftsmanship deserves nothing but the best.